What’s Your Solution to Internal Corrosion?
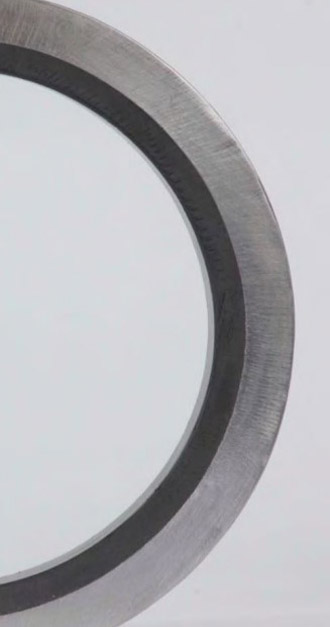
Thermoplastic Liners
Pipe with thick, flexible thermoplastic liners (i.e. HDPE, PVDF, PPS, PEX, PEEK) provides one of the safest ways to transport corrosive commodities.
Thermoplastic lined pipe is used for offshore and onshore oil production, mining slurries, and other aggressive applications.
Welded joint connections are often desired or required, particularly for offshore pipelines.
How It Works
Thermoplastic polymer sleeve bridges the weld zone.
Permits standard full-penetration weld of carbon steel pipe.
Faster joint assembly than any other welded joint solution.
Prevents welding heat from damaging the plastic liner.
Prevents liquids from reaching the bare steel behind the liner.
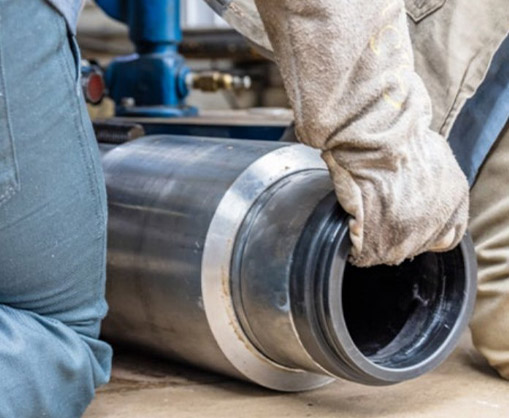


How It Works
Liner pulled through pipe and locked to pipe wall
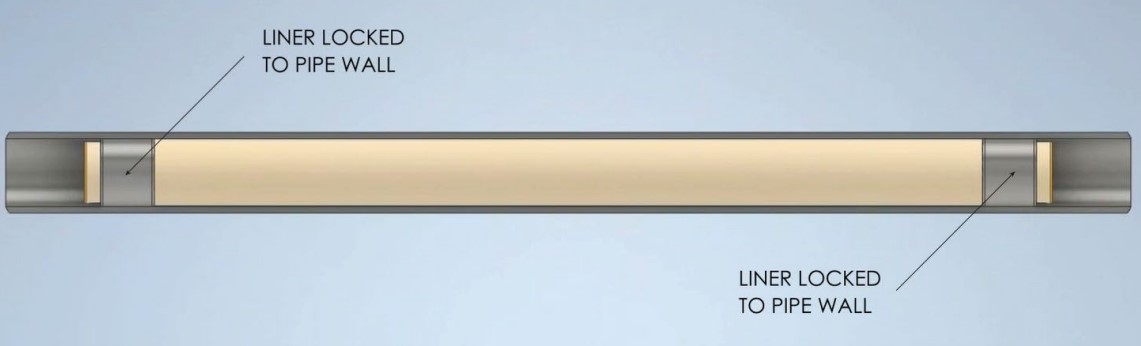
Locking rings withstand >30 tons of force, ensuring liner will not move.
Liner insertion and locking to pipe wall may be done in shop, spool base, or in field.
Liner may be installed in any length of pipe section (12m or as long as currently possible).
How It Works
SealSleeve™ inserted into pipe ends during pipeline construction & girth weld performed
Hydrostatic Pressure Tests
Hydrostatic pressure tests up to 500 bar (7,200 psi), without a weld.
The higher the pressure, the tighter the seal.