The Solution
Client engineers established an extensive testing protocol for internal sleeves. They wanted to verify there was not any sleeve coating or seal damage from the high temperatures involved with welding thick-wall small diameter pipe. They also wanted proof that the corrosive water was not going to reach the bare steel of the weld zone at the hydrostatic pressure test of 345 bar (5,000 psi).
FlexSleeve® resists welding heat better than competitor sleeves due to its width, and its self-energizing bore seals only get tighter as the pressure increases. The superior performance observed during testing at the client location led the engineers to specify FlexSleeve® for this critical water injection line, underscoring their dedication to protecting their infrastructure and the environment.
The contractor and client were satisfied with the FlexSleeve® installation and welding process and are looking forward to constructing more pipelines using LPS technology.
The Details
Pipeline: 6”, 4”, 3” dia. sch. 160 seamless pipe 32°C (90°F) operating temp10.3 kilometers (6.4 miles) total
Internal Lining: Sherwin Williams Pipeclad 702G fusion bonded epoxy
LPS Product/Qty: 868 ea. FlexSleeve® XW (extra wide)
Owner/Contractor: Confidential – inquire with LPS for more information
Location/Date: South America, November 2023
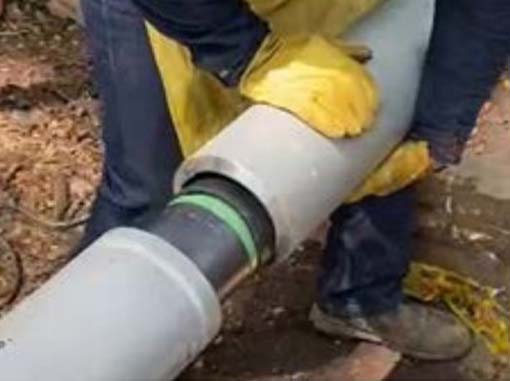
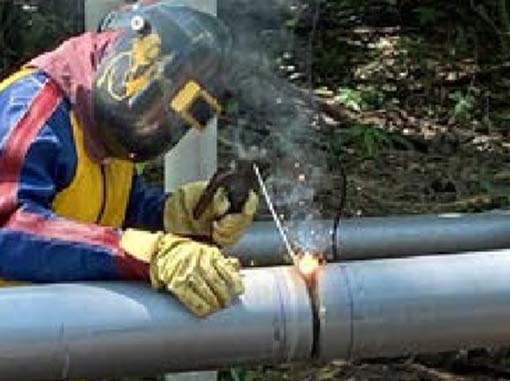
Not only does FlexSleeve® protect the weld zone better than competitor sleeves, joint assembly and welding proved to be fast and easy for the contractor.